Our Proven Process
Our Proven Process Ensures Quality
Our team prides itself on the quality of our services. We meticulously follow proven processes to maintain our ISO 9001:2015 certification and consistently bring our customers the highest quality finished products possible.
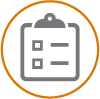
Customer Data And Reporting
Products and equipment entering our facility are tracked and reported by serial number, model number and/or first level autopsy as required by our customers. This information is provided to our customers, who determine if their product/equipment will be immediately inventoried or disassembled.

Visual Inspection
Each item is visually inspected using a multi-point checklist before it is sorted for reuse or recycling.
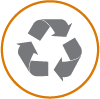
Reuse Or Recycle
Parts that cannot be reused or refurbished are sorted and sent for recycling or returned to our customer. Parts that will be reused are forwarded to our remanufacturing area, where they are cleaned, painted and returned to near perfect OEM status. These parts are then moved to the final inspection and testing station.
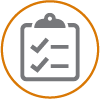
Inspect And Test
All parts that have been remanufactured are precision- inspected and tested for quality per customer specifications. Parts that fail their inspection and testing at any point are recycled or returned to our customer.
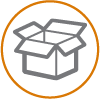
Build And Ship Kits
When parts reach the end of our process, they can be packaged individually or in kits for on-demand shipping. We work with a variety of freight carriers for local, national and international shipping.
Adhering To The Highest Standards
In addition to maintaining our ISO 9001:2015 certification, we adhere to all relevant regulations set by the Occupational Safety and Health Administration (OSHA) and the U.S. Environmental Protection Agency (EPA). This allows us to safely work with a variety of hazardous materials, including lead, beryllium, solvents and chemicals.